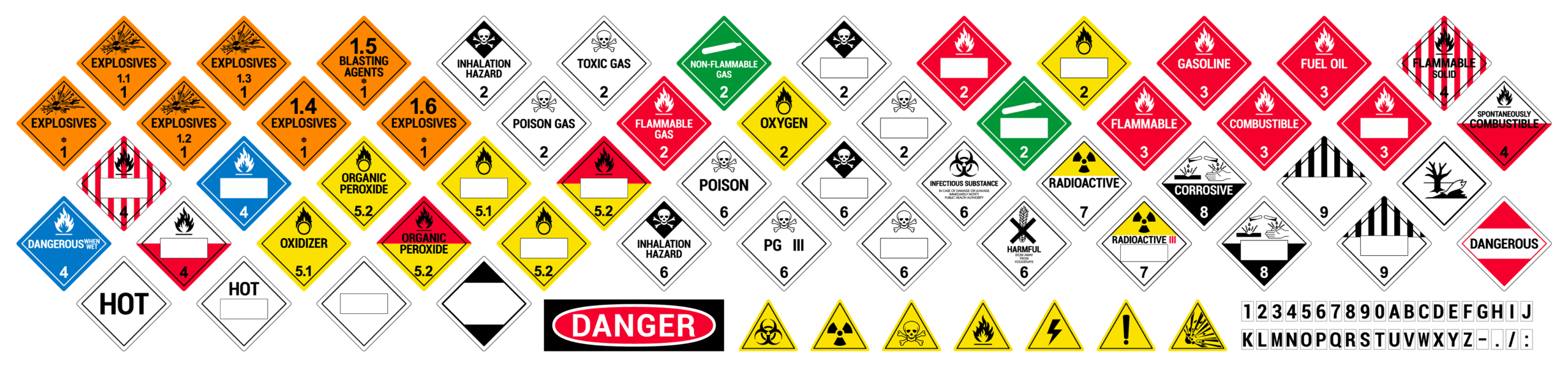
Safety for people, the environment and business: How digital checklists support and optimize hazardous goods loading at the same time
Dangerous goods transports are subject to strict regulations in Germany, no matter how they are carried out. To ensure that nothing happens on the way, the utmost care is the top priority during loading. Digital checklists support the shipper optimally in this process: They are workflow-driven, ensure the completeness, accuracy and plausibility of the data and make reporting and documentation transparent and (audit) safe.
The be-all and end-all when transporting dangerous goods is meticulous preparation – and that begins with the loading of the dangerous goods. Using checklists, shippers check in detail and carefully whether all regulations relating to the filling systems, transport units, drivers and vehicles are being observed. Unfortunately, working with paper increases the risk of misstatements, omissions or illegibility, which can have serious consequences should a disruption or accident occur during transport. Digital checklists, which the shipper fills out on his tablet or smartphone, consistently counteract possible sources of error, as the use case of a refinery shows.
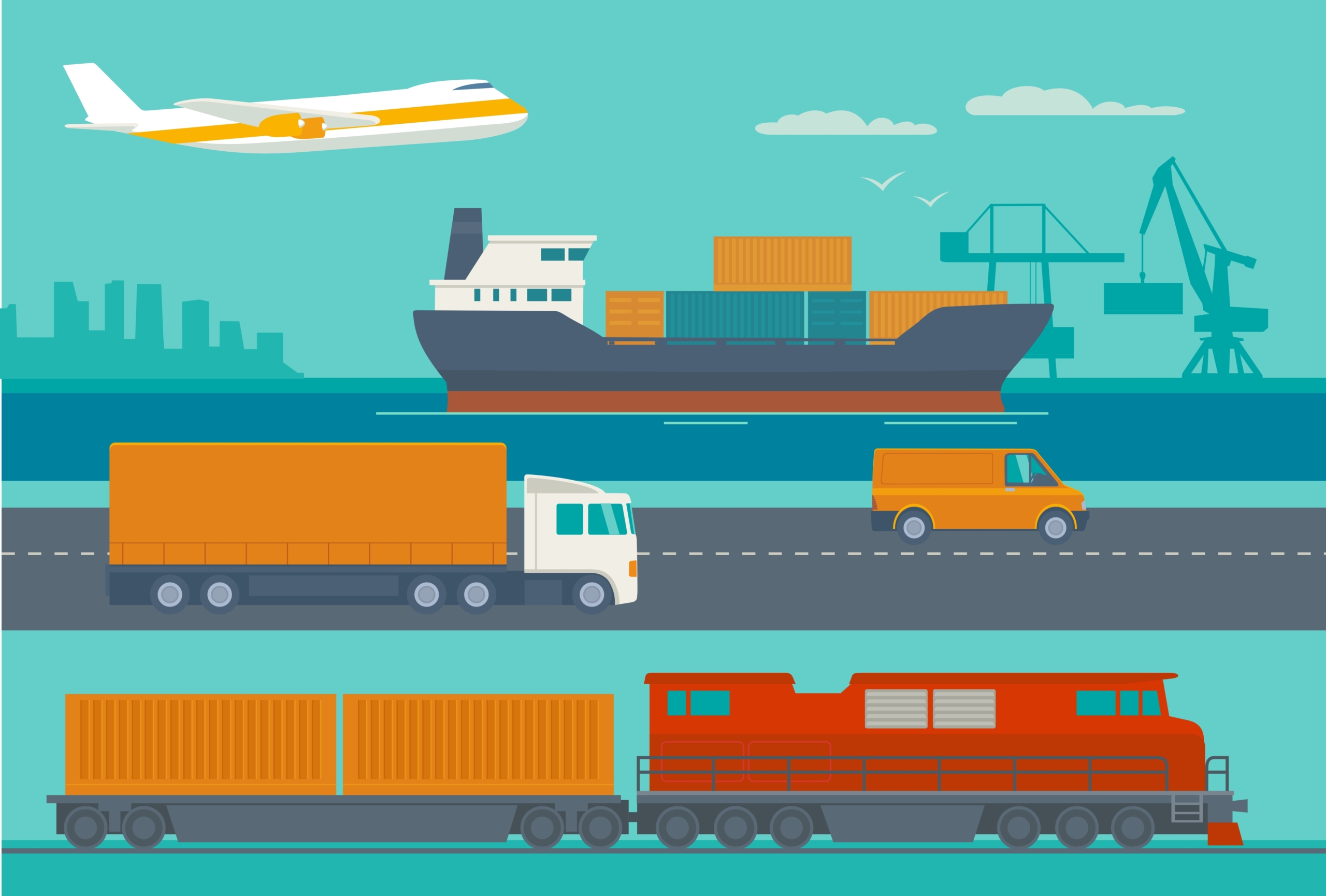
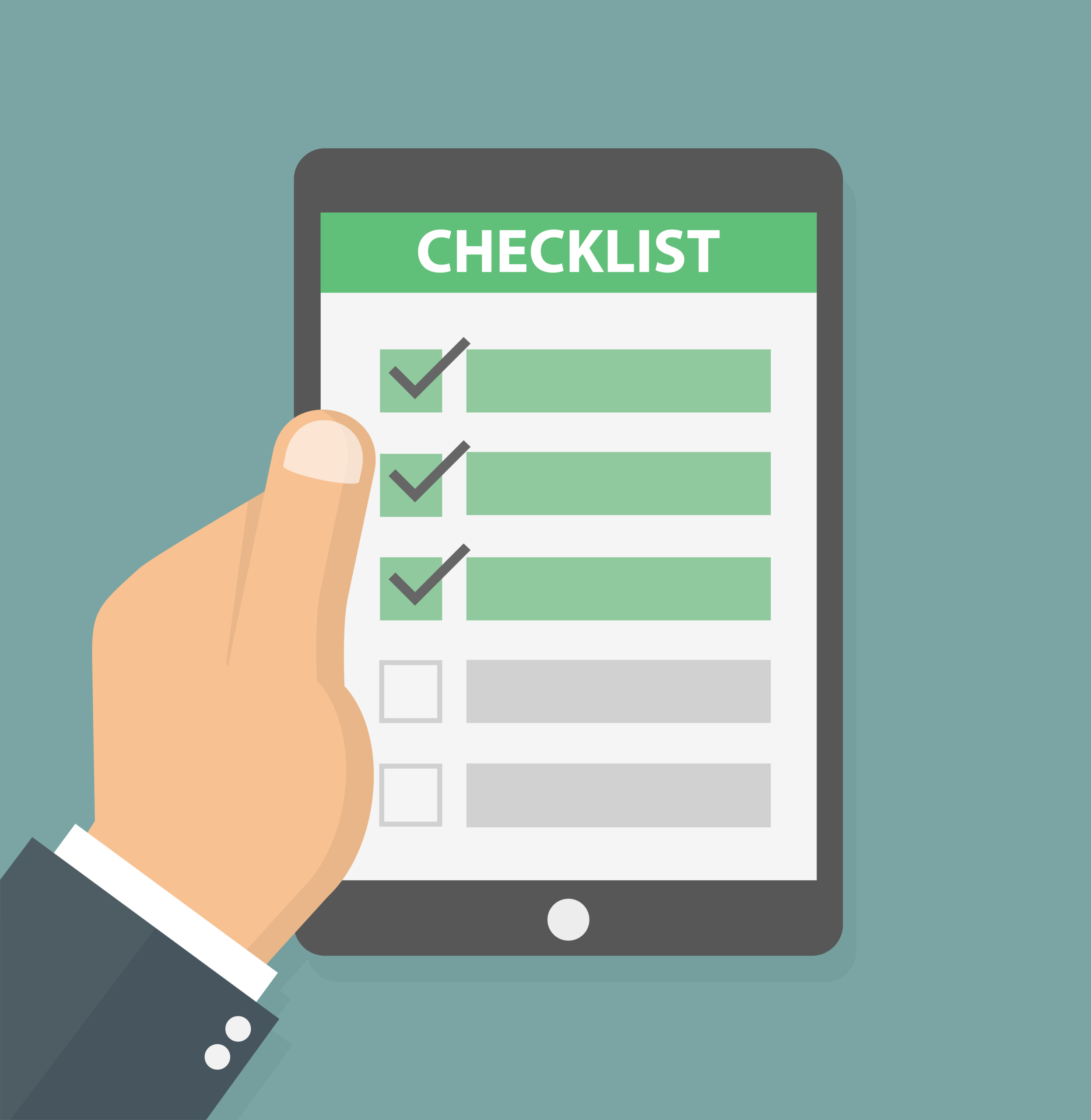
The correct checklist for the hazardous substance to be loaded
Every year, the company carries out thousands of hazardous goods shipments, many of them by rail. It uses its own digital checklist for each individual hazardous substance, which is maintained centrally and distributed to the shippers via email link or app and is therefore always up to date with the latest legal status. In this way, the shipper always has the correct checklist in the currently valid version at hand on site and therefore does not run the risk of carrying out his check on an outdated version. This also saves him time and walking distances if he does not have a certain checklist with him and he would otherwise have to run back to fetch it or request it by telephone.
Is the freight car number correct?
Since incorrect information sometimes occurred in the hectic everyday life or individual points were forgotten, plausibility checks were linked to individual fields of the digital checklist. For example, when entering the 12-digit UIC freight wagon number, the self-check digit is automatically calculated using the Luhn algorithm. If this is not correct, the shipper is made aware of the error. Mandatory fields and automatically pre-filled fields such as date, time and name of the shipper prevent gaps and save time when filling out. They also limit the scope for manipulation. A digital checklist can also only be completed when all items have been filled in or ticked off and the document has been signed. If the shipper notices something that he would also like to document, he can take a photo with his smartphone and integrate it into the checklist.
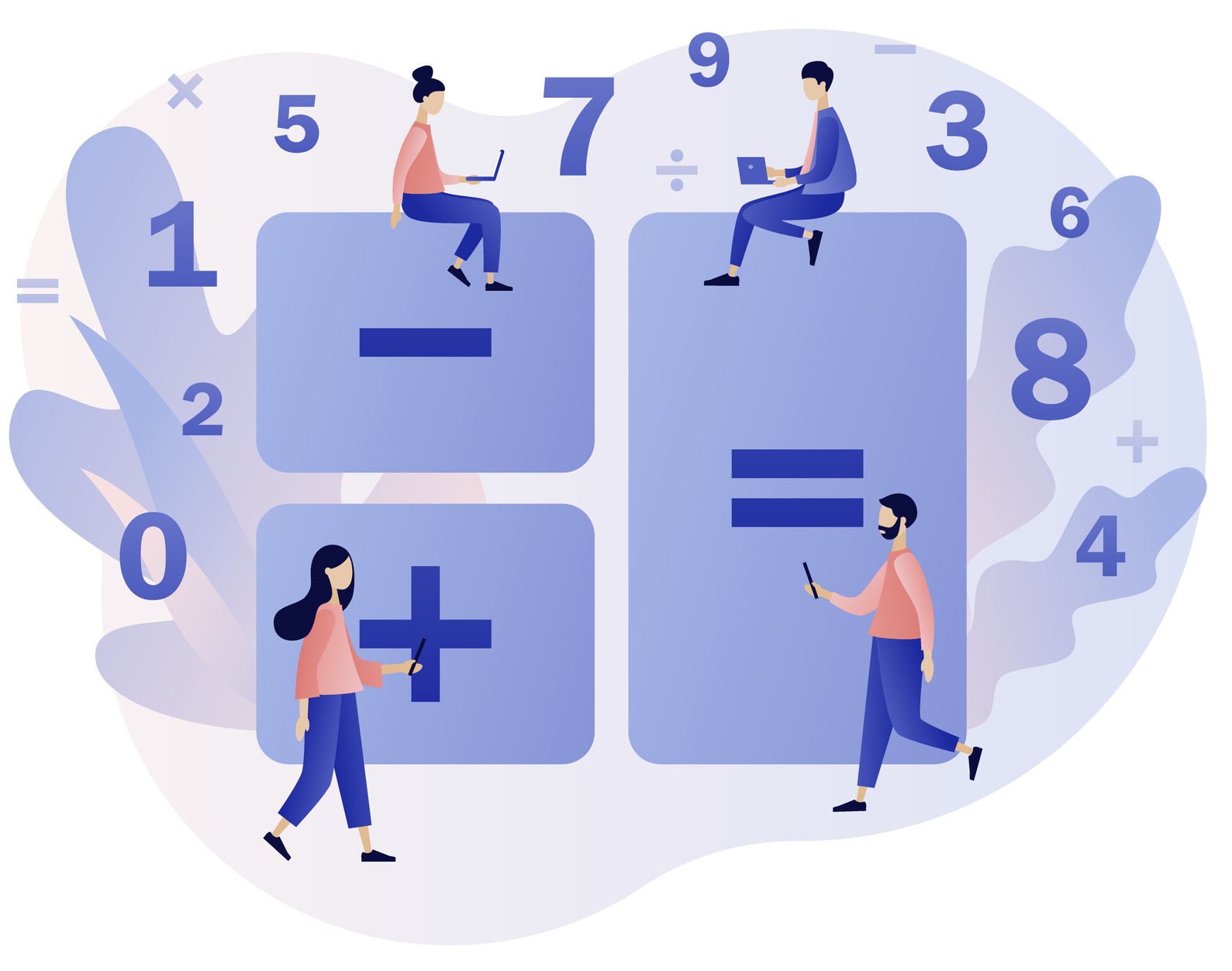
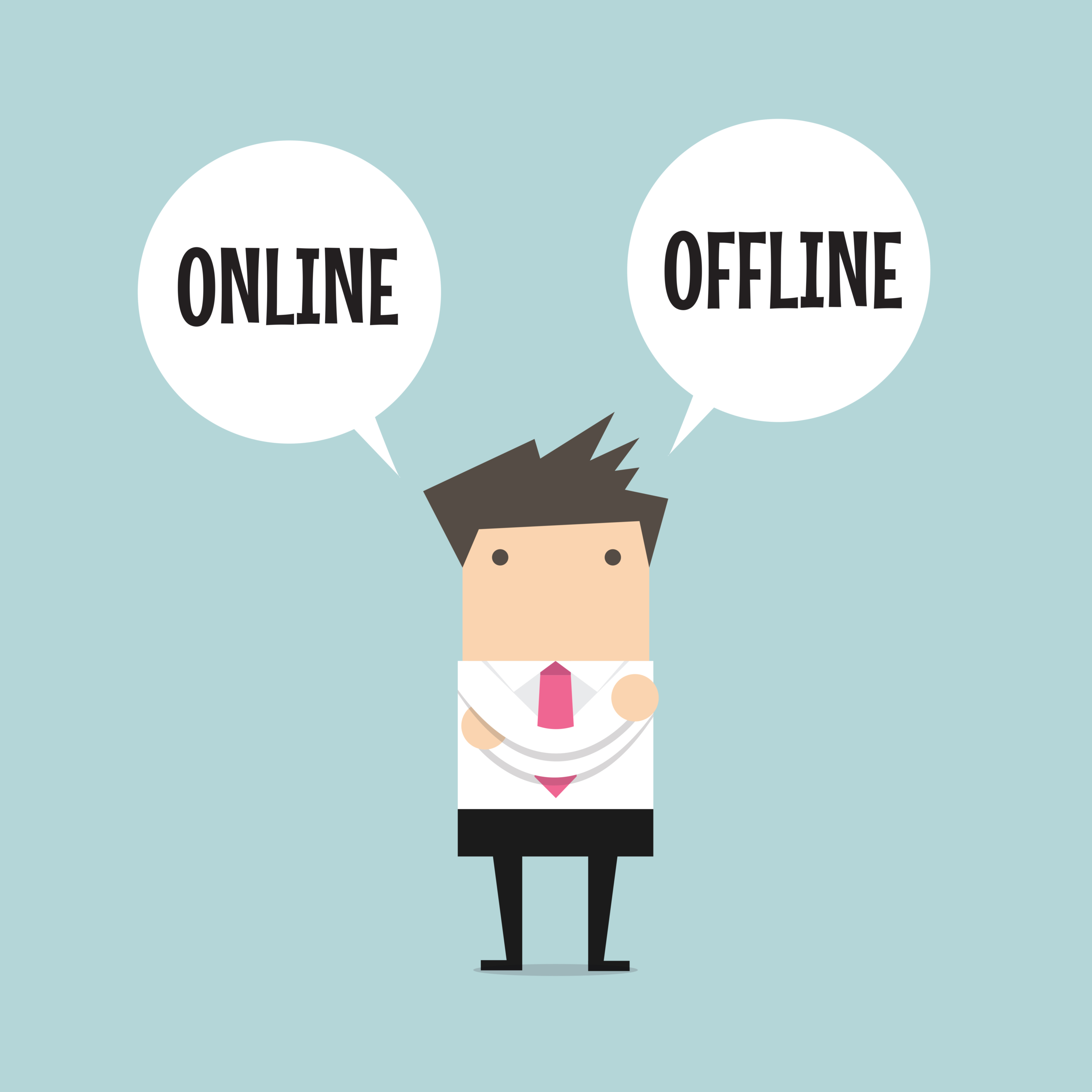
Complete online and offline
The digital checklists not only ensure maximum accuracy during the loading process, they also support and optimize upstream and downstream processes. For example, they make printers, ink and paper superfluous, minimize travel times and maintenance costs, and since many employees today have a smartphone or tablet anyway, no major investment in hardware is necessary. The digital checklists can be filled out both online and offline, the synchronization takes place automatically as soon as (mobile) internet is available again. You will be forwarded automatically after completion, so that the entire scanning process, for example, is no longer necessary. The completed checklists are stored centrally, information is transparent for all authorized employees and can be found quickly using the search function. All data is stored in an audit-proof manner as clear evidence of who documented what and when.
Avoid penalties through legal certainty
Overall, digital checklists improve the safety of people and the environment in the company, as a result there are fewer claims and penalties from the authorities, and there are fewer internal problems because documents are filled out correctly more often.
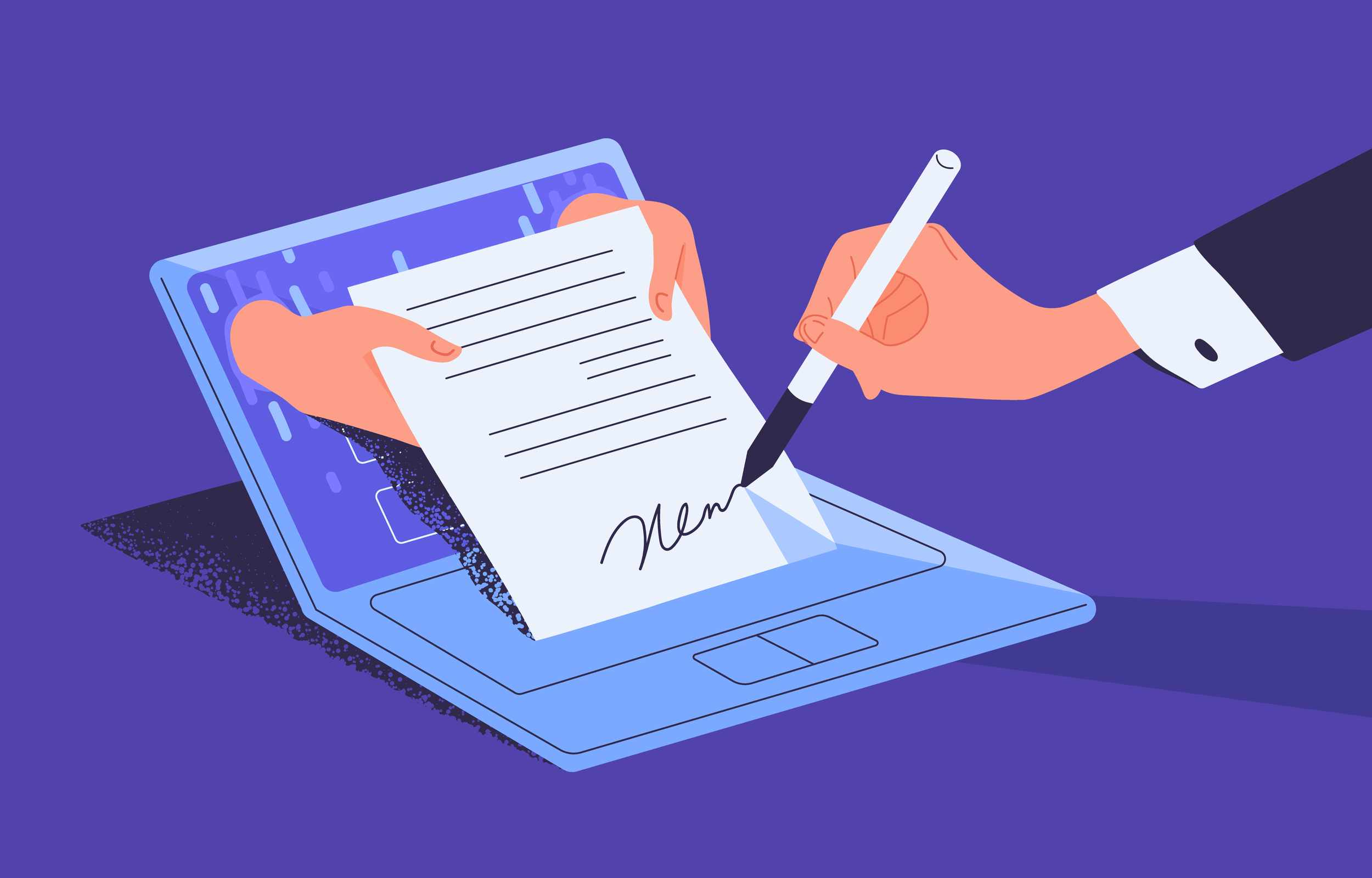
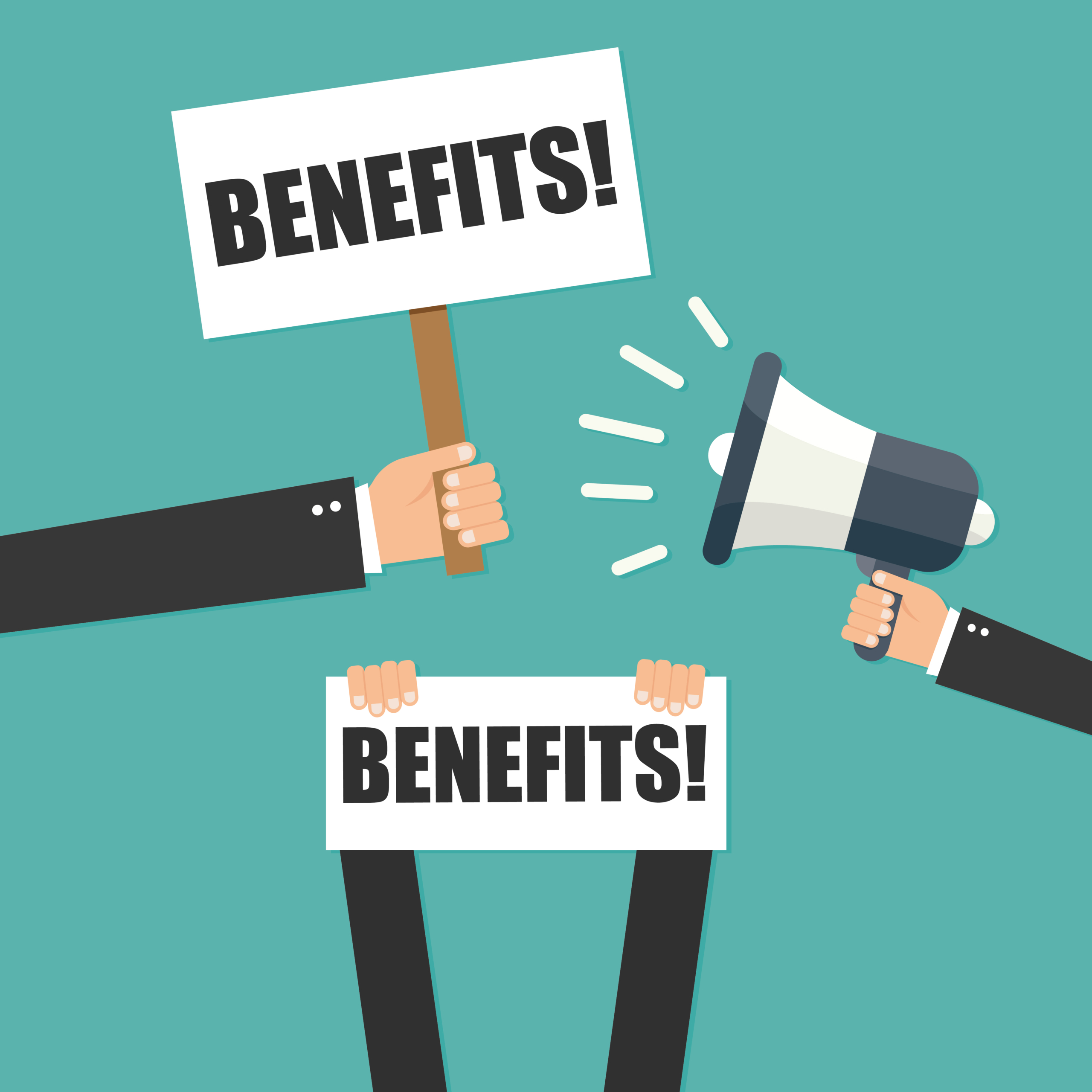
your added value
• More security when entering. Plausibility checks, e.g. for tank car numbers, fewer incorrect entries, documentation with pictures on site, checking for completeness
• Greater legal certainty. Clear proof of who documented what and when, less room for manipulation, and time savings for employees
• More time for value-adding activities. Automatic mail routing or storage in the document management system, so that the entire scanning process is no longer necessary and saving is also automated.
• More efficiency. Printer ink and paper are no longer wasted, minimizing travel times, minimizing printer maintenance, finding information quickly with a search and soon also very easily using the KWG number
• More flexibility. Access to the solution via browser and link, view a wide range of information regardless of location or make adjustments to checklists.
Checkware supports you in conducting inspections as part of the operational process
Finito
Shift booksFinito
Shift books, bypass books, instructions and information boards with real-time machine data.Checkware
Checklists and workflowsEmplovis
Personnel planning & skill managementEmplovis
Shift planning with SAP interface. Skill management. Vario shifts, shift changes, overtime registration, vacation requests.Synoset
Asset and service managementSynoset
Process control, resource management, maintenance plans, property management, asset management, ticketing, project control.Part of your connected worker environment
Synoset is used by many customers as a high-performance single product for the administration of notices and requirements.
Synoset also works seamlessly with the three other products of New Solutions Connected Worker Platform Finito, Checkware and Emplovis together:
- When using the Finito shift book Tasks from the management of notices and conditions can be integrated into shift operation and automatically assigned directly to shift workers.
- When using the Checkware All tasks can also be sent as self-created checklists directly to the mobile devices of the production employees
- When integrating Emplovis Employee qualifications and certifications can be linked to the circulation management
Please contact us for more information on Synoset here .
Zufriedene Anwender
So habe ich in kürzester Zeit einen Überblick, ob es zuletzt Auffälligkeiten oder Veränderungen im Produktionsablauf gab oder ob etwas Sicherheitsrelevantes passiert ist. Ich kann unmittelbar reagieren.
New Solutions ist den Umgang mit produzierenden Unternehmen gewöhnt. Die Spezialisten sprechen dieselbe Sprache wie wir und wissen auch, welche Risiken in Änderungen an solchen Systemen stecken.
Für das Programm Finito Digital Shift Book von der New Solutions GmbH haben wir uns wegen des Funktionsumfangs und des guten Preis-Leistungsverhältnisses entschieden. Außerdem ist die Lösung intuitiv und damit sehr einfach zu bedienen, das hat uns gut gefallen.
Dass ein vergleichsweise günstiges Standardprodukt wie Finito sich so anpassungs- und erweiterungsfähig zeigen würde … hat mich positiv überrascht.